Analyze
The Analyze in DMAIC is about finding the root causes of the problem; we are attacking them. Often there is one primary cause that is driving most of the unwanted variation, and controlling or eliminating this cause is all that is needed. In the analyze phase the team reviews data collected during the measured phase. The goal is to narrow down and verify root causes of waste and defects.
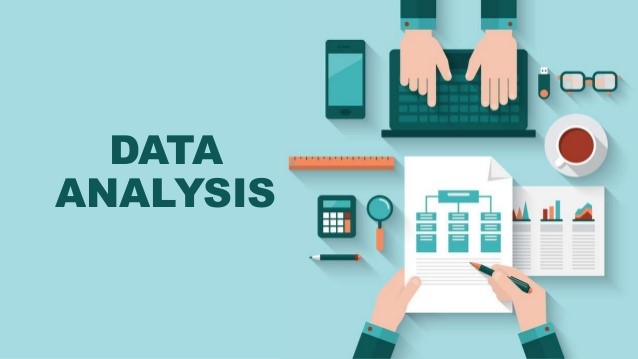
Data analysis is also called cause analysis. It attempts to find defects that are derived from the sources of information or work generation. After finding the root cause of the problem, attempts are made to resolve the problem before we expect to eliminate defects from the product.
Three Steps to Root Cause Analysis
The open step: During this phase, the project team brainstorms all the possible explanations for current sigma performance.
The narrow step: During this phase, the project team narrows the list of possible explanations for current sigma performance.
The close step: During this phase, the project team validates the narrowed list of explanations that explain sigma performance.
Process Analysis
Analyze the numbers to find out how well or poorly the processes are working, compared to what's possible and what the competition is doing.
Process analysis includes creating a more detailed process map, and analyzing the more detailed map, where the greatest inefficiencies exist.
The source analysis is often difficult to distinguish from process analysis. The process refers to the precise movement of materials, information, or requests from one place to another.
Data Analysis
Use of measures and data (those already collected or new data gathered in the analyze phase) to discern patterns, tendencies or other factors about the problem that either suggests or prove/disprove possible cause of the problem.
The data itself may have defect. There may be a case when products or deliverables do not provide all the needed information. Hence data is analyzed to find out defects and attempts are made to resolve the problem before we expect to eliminate defects from the product.
Resource Analysis
We also need to ensure that employees are properly trained in all departments that affect the process. If training is inadequate, you want to identify that as a cause of defects.
Other resources include raw materials needed to manufacture, process, and deliver the goods. For example, if the Accounting Department is not paying vendor bills on time and. Consequently, the vendor holds up a shipment of shipping supplies, it becomes a resource problem.
Communication analysis
One problem common to most processes high in defects is poor communication. The classic interaction between a customer and a retail store is worth studying because many of the common communication problems are apparent in this case.The same types of problems occur with internal customers as well, even though we may not recognize the sequence of events as a customer service problem.
The exercise of looking at issues from both points of view is instructive. A vendor wants payment according to agreed-upon terms, but the Accounting Department wants to make its batch processing uniform and efficient. Between these types of groups, such disconnects demonstrate the importance of communication analysis.
Key Features:
- Perform multi-vari analysis
- Complete FMEA
- Identity potential critical inputs
- Develop plan for next phase
Key Tools:
- Ishikawa diagram
- Cause -and- effect and 5 whys
- Pareto chart
- Brainstorming
Key Activities:
- Stratify data to identify the underlying problems
- Identify root causes
- Validate root causes
What will be done in Analyze phase?
- Understand the old system
- Identify how the old system can be improved
- Develop specification for the new system
Identify solution to overcome the effect of root cause
For each of the root causes identified in the Analyze phase, the Lean Six Sigma Team uses an apt structured or unstructured brainstorming method to generate various alternatives to overcome the problem. These techniques may include Channeling, Anti-solutions, Analogy, Wishful thinking, Random word stimulus methods, etc.
If there are too many options that the team has identified, then a variety of solution screening methods can be used to select the best solution for implementation. These screening methods include NGT (Nominal Group Technique), N/3 Voting, Criteria Based Matrix (CBT), etc.
Proposed solutions can be a new process, technology change, policy changes, alterations of inputs, measurement system refinement, customer, employee or vendor education, etc. In such cases, either revised process map, future state value stream mapping, etc., may need to be proceeded.
The solution that the team has selected should directly impact the CTQ of the project. Six Sigma Green Belt should validate this.